Is Continuous Improvement the Same as Lean
" Lean" is considered to be a philosophy of continuous improvement.
What is Lean Continuous Improvement?
Lean Continuous Improvement is defined as a method for identifying opportunities for streamlining work, reducing waste, and increasing productivity. By observing Lean Continuous Improvement best practices, manufacturers can figure out ways to continue business as usual while analyzing improvement opportunities along the way.
Consider a simple task of watering a garden of plants.
If you have to water one plant, the task seems quite simple to accomplish. Now imagine watering a garden of fifty plants. This might need some planning and coordination to sequence the plants and plan the quantity of water needed for each pot. Now if you have to water all fifty plants twice a day, for one full week, this would need more coordination and better planning. It is natural that the more things we need to coordinate, the more chances we have of breakdowns.
The more complicated processes get, the higher the possibility for inefficiencies to set in. These inefficiencies can waste time, and cost money and labor which can in turn impact the total profits for an organization.
Lean continuous improvement cuts down these inefficiencies and directly implies the reduction of wastes and enhancement of specific processes. A lean manufacturing set up always focuses on increasing customer value, reducing waste and optimizing factory operations.
In addition to reducing wastes and process improvement, Lean is also about building a culture of continuous improvement. One where workers pursue opportunities to improve their work and share ideas for continuous improvement.
What are the Five Principles of Lean Manufacturing?
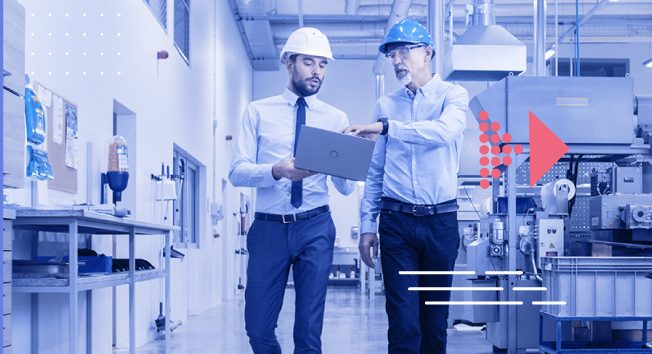
1. VALUE
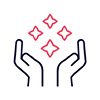
The first step toward Lean Manufacturing is to establish an understanding of what value the customer assigns to products and services. This directly determines what the customer will pay for them. By ascertaining the value, manufacturers can create the top-down target price to calculate the cost to produce the products and services. This is where manufacturers focus on eliminating waste to deliver this expected value, to finally earn the highest possible revenue outcomes.
2. VALUE STREAM
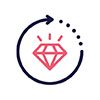
The value stream refers to the sum total of the product's entire life-cycle starting from the raw materials until the stage of the customer's use and final disposal of the product. Lean principles aim at eliminating as much waste as possible and for this, there needs to be a clear understanding of the value stream. Data-driven manufacturing processes are examined to figure out the value-added and those steps, materials, features, and movements that do not add value are eliminated. It is also observed that many of these steps might unambiguously create value. Many of these steps will also end up creating no value but cannot be avoided due to the adoption of certain technologies. Also, several additional steps that could create value may be immediately avoidable.
3. FLOW
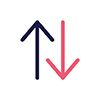
The next principle of Lean continuous improvement is about understanding the flow which can help in the elimination of waste. In case there is an abrupt halt in the value stream from moving forward at any point, this waste becomes the inevitable by-product. This principle of flow is about creating a value chain with zero interruption in the production process and is a state where each activity is fully in sync with every other.
4. PULL
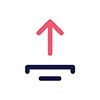
This principle of pull ensures adequate flow by making sure that nothing is produced ahead of time, building up work-in-process inventory, and stopping the synchronized flow. Instead of using the traditional manufacturing approach of allocating workload based on a forecast and pre-decided schedule, the pull approach indicates that nothing is made until the customer actually orders it. This would however need a lot of flexibility and a brief design to deliver cycle time. There is also a need to establish an effective communication approach at each step of the value chain.
5. PERFECTION

Lean manufacturing is designed based on the ultimate goal of perfection. This happens step by step as lean continuous improvements tackle the root causes of quality problems and production waste. This relentless pursuit of perfection can help manufacturers dig deeper, measure more accurately, and change more often than their competitors.
The Benefits of Lean Continuous Improvement
1. MORE EFFICIENT OPERATIONS
Lean continuous improvement directly creates higher efficiency across factory operations as wasted processes and components are eliminated immediately. Without unnecessary tasks and time-consuming activities, manufacturing processes become more productive and effective.
2. SHORTER DELIVERY CYCLES
When products are produced in a shorter time, they end up reaching customers sooner than before. This shortened lead time can not only result in generating more orders but also utilizing resources productively for higher output.
3. REDUCED ERROR RATE
Lean continuous improvement process results in refining existing production processes. This means the same procedure is now fine-tuned to perform better and this gets even more efficient over a period of time. As a result, the number of errors automatically comes down.
Refined process = better process = fewer mistakes = better quality control.
4. BETTER QUALITY
When processes are improved, this results in achieving quality improvement which has multiple benefits. So, there are fewer mistakes, lesser downtime, reduced product recalls, and enhancement in customer experiences. There also is an increase in brand perception and greater reliability of your finished products and services.
5. HIGHER SCOPE FOR INNOVATION
Other than just eliminating wastes, manufacturers also find a better way of doing the same thing. Re-inventing what exists or innovating with something new can create a seismic shift in existing processes. This not only increases process efficiencies and can also generate new revenue streams.
6. LOWER OPERATING COSTS
This is one of the most obvious benefits of lean. When manufacturers produce more products in less time with fewer errors, operating costs directly come down. This is complemented by savings in labor time and expenses. Matrical costs also come down and finally waste is completely eliminated.
7. GREATER PROFITABILITY
Along with lower costs, manufacturers can easily work towards greater profitability. Also, a better product/ service quality implies the ability to charge a premium for an existing product. When you increase your profits, you automatically have a better cash flow to help further finance your business operations.
8. IMPROVED CUSTOMER EXPERIENCE
With a better work culture and happier employees, manufacturers can easily enhance the overall customer experience. A greater product quality, fewer recalls and accelerated delivery cycles also add to this experience.
A Guide to Implement Lean Continuous Improvement
Lean Continuous Improvement has to be looked at as an ongoing improvement process to constantly improve the manufacturing of products, services, or processes. This is defined as a six-step systematic approach to plan, sequence and implement improvement efforts within the organization.
IDENTIFY THE IMPROVEMENT OPPORTUNITY:
The first step is to select the appropriate process for improvement. Manufacturers then need to evaluate this process and select an appropriate challenge or a problem to be tackled.
ANALYZE:
The next step is to identify the root cause for this challenge.
TAKE ACTION:
After analysis, it is important to plan and implement necessary actions that correct these root causes.
CONFIRM THE STUDY RESULTS:
Next is to confirm the specific actions that need to be taken to achieve this target.
STANDARDIZE THE FINAL SOLUTION:
It is important to standardize the possible solution to ensure the improved level of performance is maintained.
PLAN FOR FUTURE:
Finally,plan what needs to be done with any possible remaining problems and evaluate the team's effectiveness by setting a target for improvement
What is the Difference Between Lean Manufacturing and Continuous Improvement?
While Lean Manufacturing focuses on eliminating waste, Continuous Improvement is more bottom-up in approach. Lean Manufacturing can be directly achieved by a business decision to work toward a specific goal. Some business decisions which could be under the guise of "Lean Manufacturing", can lead to a strain on the production workforce or employees who are not as skilled and taking longer to perform certain processes which can put them and the factory manufacturing operations management at a higher risk. This can result in top-down work stress and some conflict between management and production teams.
Continuous Improvement aims at encouraging and supporting shop floor employees to identify solutions for improvements in the manufacturing process. It puts complete ownership on production employees which makes them feel more valued and listened to, thereby improving the relationship between the shop floor and management team. Also, when their recommendations are actually implemented, it boosts their sense of pride and they are more open to changes in on-going processes for continuous improvement.
Artificial Intelligence and Lean Continuous Improvement
Artificial intelligence (AI) enables greater connectivity between people, information, and machines and this helps improve how manufacturers optimize products and processes. Similar to the benefits derived from Lean Management principles, AI also proves to be the next evolutionary step in productivity advancement.
AI helps with continuous optimization, just like continuous improvement and a commitment to constant change, which are important facets of Lean philosophy. It is therefore important for manufacturers to incorporate Lean principles complemented with AI, as they offset some traditional roles of humans while integrating with AI technology.
It is known that the use of AI can reduce conversion costs by up to 20%, with up to 70% of the cost reduction resulting from higher workforce productivity. Combining AI with Lean can enable manufacturers to create a new company culture, ensuring better operations and more flexible workflow for employees as they take up new responsibilities and transition into new roles.
One such strategic area that Lean Continuous Manufacturing focuses on is eliminating operational bottlenecks which can directly help eliminate the waste arising from production processes. ThroughPut's Bottleneck Elimination Software ELI, helps operations managers achieve unprecedented AI-driven Productivity & Operational Excellence. ELI helps meet and beat supply chain goals by nailing-down bottlenecks & eliminating waste to achieve end-to-end supply chain efficiencies.
Say no to bottlenecks, say no to waste.
Source: https://throughput.world/blog/lean-continuous-improvement/
0 Response to "Is Continuous Improvement the Same as Lean"
Post a Comment